Metalworking is the process of shaping, cutting, and manipulating metal to create objects, structures, and parts. This technique has been used for centuries, dating back to the Bronze Age, and has evolved over time to become a vital aspect of modern industry. In this article, we highlight the top 10 interesting facts about the process and history of metalworking that you will want to discover more about.
1. The first metal to be widely used in metalworking was copper, followed by bronze and iron
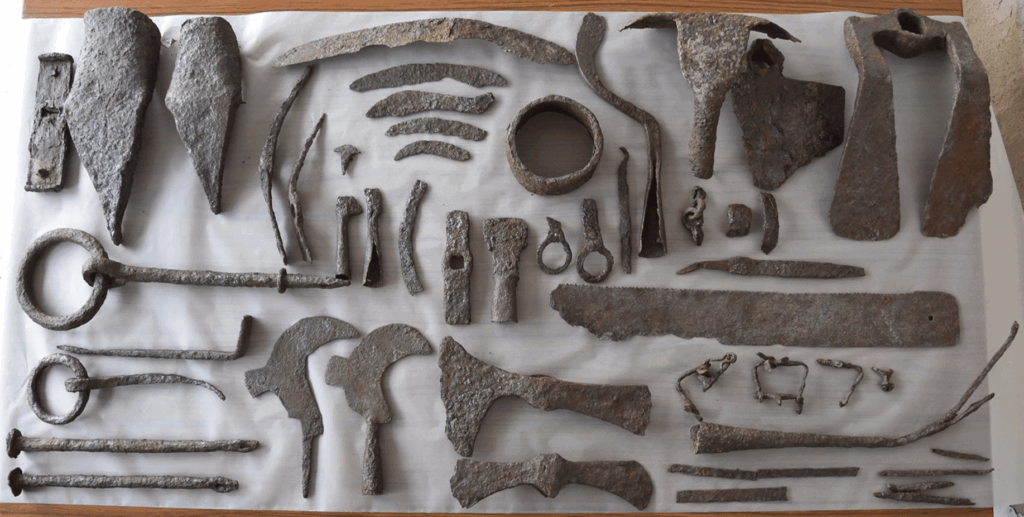
Copper was the first metal applied in metalworking due to its unique properties. It is relatively soft, ductile, and has a low melting point, making it easy to work with using basic metalworking tools. Copper was discovered around 8000 BCE and was used by early civilizations to create instruments, weapons, and jewelry.
Bronze, which is an alloy of copper and tin, was developed around 3500 BCE and quickly became the preferred metal. Bronze was harder and more durable than copper, making it ideal for creating weapons and tools, it also had a lower melting point than iron.
Iron was first used in metalworking around 1200 BCE and quickly replaced bronze as the preferred metal. This material is much harder and more durable than bronze, but it is also more challenging to work with due to its higher melting point. Ironworking techniques continued to evolve over time, leading to the development of steel, which is an alloy of iron and carbon.
2. Metalworking techniques were first developed in the Middle East around 4000 BCE
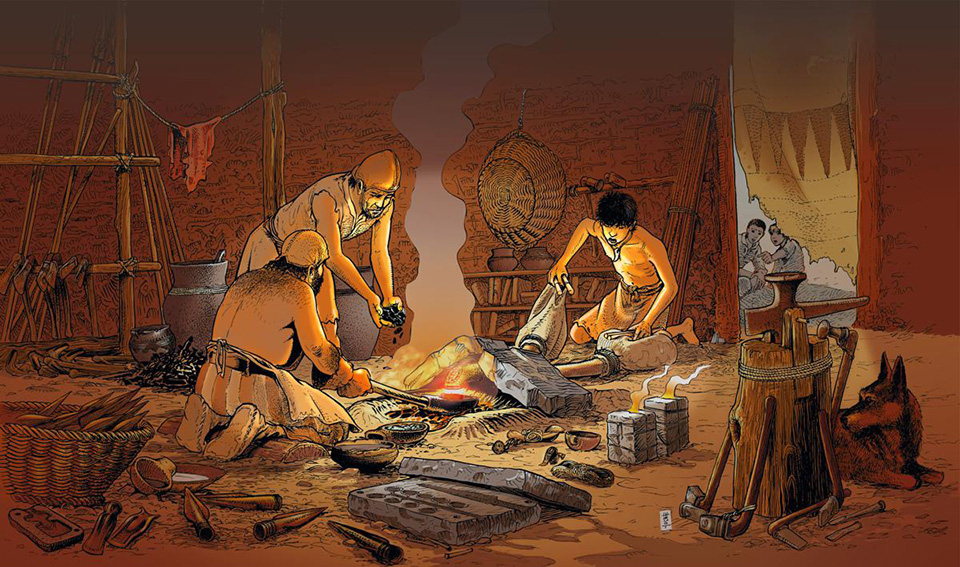
One of the key inventions that revolutionized the metalworking industry was the furnace. It is a device that is used to heat materials to high temperatures, melting and shaping them. The furnace lets metalworkers process materials like copper and bronze, which have low melting points, and create a range of tools, weapons, and decorative objects.
Another key invention that enhanced metalworking was the bellows. These devices are used to blow air into a fire, increasing its intensity. Their invention made it possible to achieve higher temperatures in furnaces, enabling metalworkers to process metals like iron.
The Middle East was a particularly important region for the development of metalworking techniques due to its abundant natural resources, including copper and tin. The availability of these resources, combined with the invention of the furnace and bellows, allowed the region’s metalworkers to create highly-effective techniques that are still applicable.
A shortened version of the history of metal work you can see on the scale.
- Prehistory — Making small items from copper ore.
- 2600 — 2400 BC – Use of wrought copper foil.
- 1500 — 1200 BC – Development of bronze casting.
- 1500 — 30 BC – Purification of gold.
- 900 BC — 100 AD – Use of iron.
- 540 — 500 BC – Use metal as money.
- 700 — 800 AD – Sword-making.
- 15th century – Making weapons from cast metals.
- 1810 – Creation of a tin can for storing food.
- 1910 – Producing the first aluminum foil.
- The 1950s – Development of the titanium aircraft.
3. The first metalworking industry in the United States was established in Jamestown, Virginia, in 1608
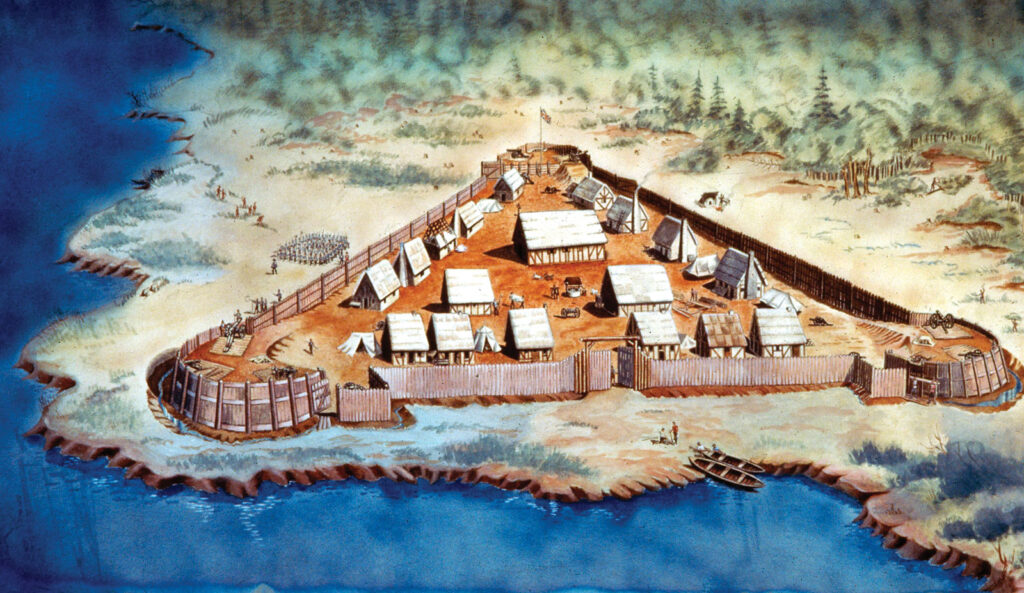
The colonists used metalworking techniques to create a range of tools, including hoes, axes, plows, and other farming implements. The establishment of the metalworking industry in Jamestown was a crucial step in the development of the United States. The industry provided the colonists with essential tools and weapons, which enabled them to establish settlements and defend themselves against external threats. Metalworking also paved the way for the development of other industries, such as manufacturing, which have become essential to the modern economy.
4. The Industrial Revolution greatly expanded the use of metalworking
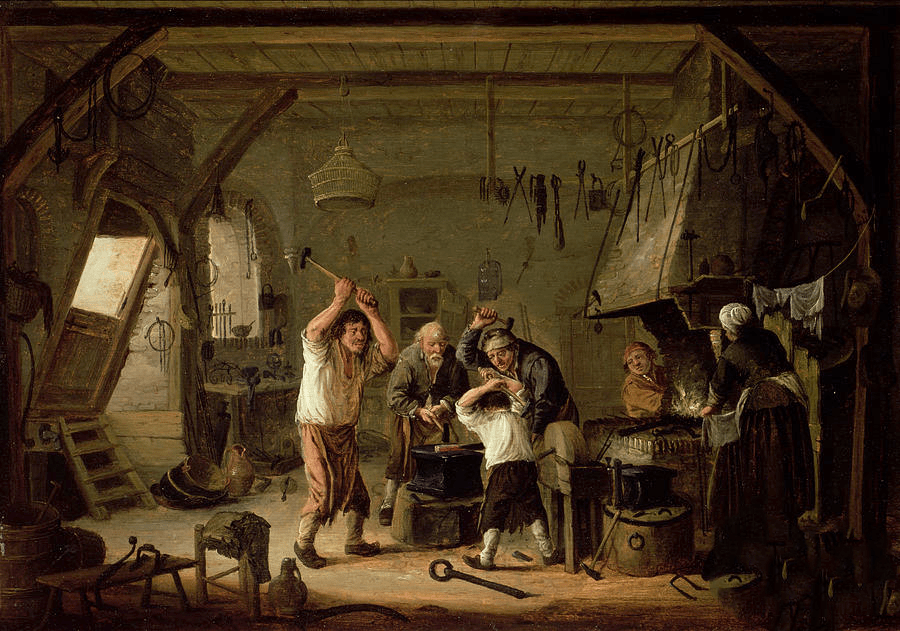
This period began in the late 18th century and influenced significant technological advancements that greatly expanded the use of metalworking solutions. The revolution marked the transition from manual labor to machine-based manufacturing, changing the way products were made.
One of the most significant advancements in metalworking during this period was the development of the Bessemer process. It was invented by Englishman Henry Bessemer in 1856 and made steel production more efficient by removing impurities from iron ore using a blast of air. This allowed manufacturers to create large quantities of high-quality steel, which was essential for the construction of buildings, bridges, and other infrastructure.
Another significant advancement was the development of interchangeable parts. This meant that individual parts of a machine could be produced in large quantities, and then assembled to create a complete machine.
5. The most commonly used metalworking techniques include arc, gas, and resistance welding
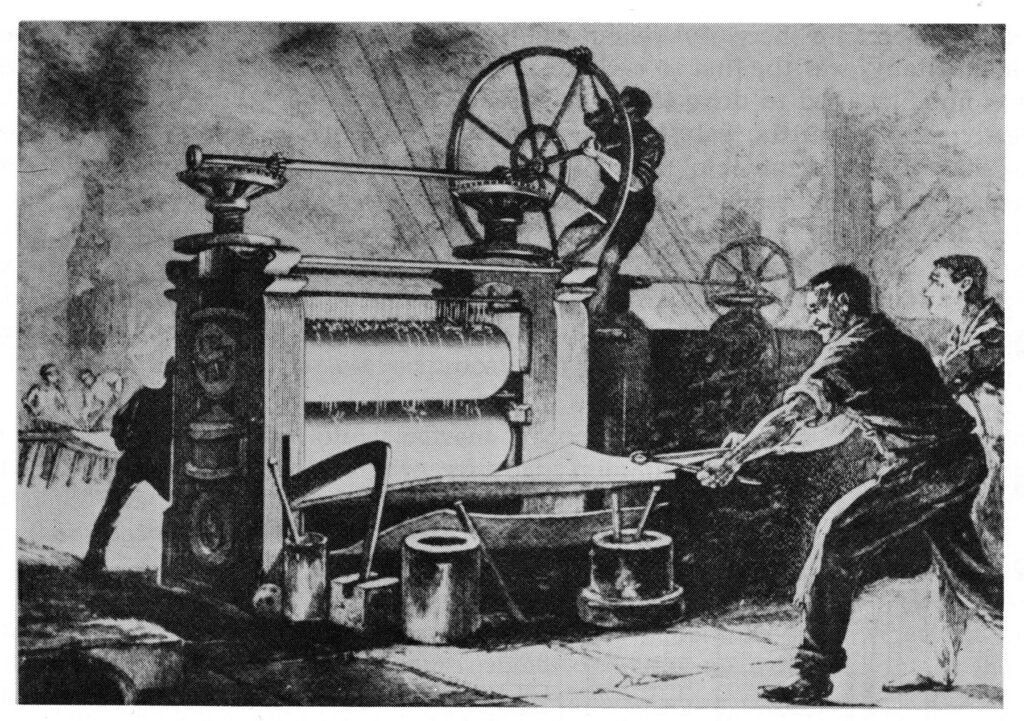
Welding has many practical applications and is used in a range of industries, including construction, manufacturing, and automotive.
- Arc welding uses an electric arc to create heat and melt the metal parts together.
- Gas welding, on the other hand, applies a flame from a gas torch to heat the metal parts and create a bond.
- Resistance welding uses the resistance of the metal itself to create heat and join the parts together.
6. To automate the manufacturing process, CNC (Computer Numerical Control) machines are widely used in metalworking
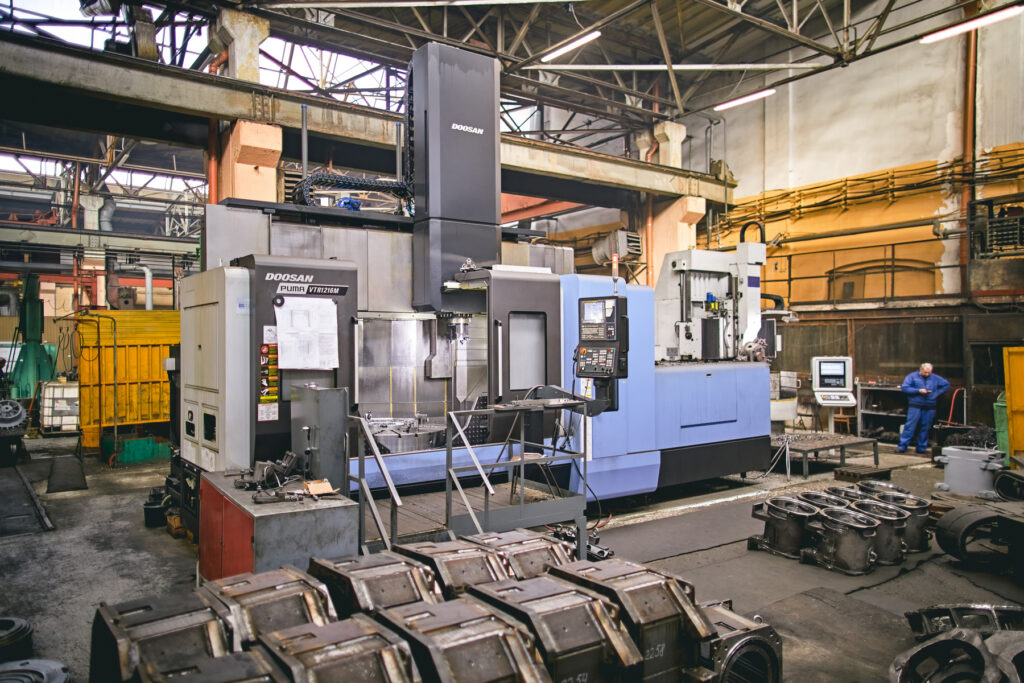
CNC machines are a type of metalworking equipment that has revolutionized the manufacturing industry. They use computer programs to control the movement of cutting tools, allowing for precise and consistent production of metal parts.
These machines can be programmed to manufacture a wide range of forms, from simple shapes to complex geometries. They are also used to create elements with a high degree of accuracy, often with tolerances of just a few thousandths of an inch. This level of precision makes CNC machines particularly handy in industries where small variations in part dimensions can have a significant impact on performance or safety.
7. Metalworking art requires a wide range of skills, including design, engineering, fabrication, and finishing
At each stage of the metalworking process, a high level of precision and attention to detail is necessary to ensure the final product meets the required standards.
- Design is the first stage of metalworking, which involves creating a blueprint for the desired product. Designers must take into account the function, strength, and durability requirements when creating the plan that will then be applied as a guide throughout the fabrication process.
- Engineering is the next stage that involves the use of math and science to solve problems and optimize the design. Engineers ensure the product is structurally sound, all components fit together perfectly, as well as the design is efficient and can be manufactured cost-effectively.
- Fabrication is the stage where the metal parts are cut, shaped, and assembled to create the final product. Fabricators must be skilled at reading and interpreting design plans, and must also have a good understanding of metallurgy and the properties of different metals.
- Finishing is the final stage of metalworking services and involves applying a surface treatment to the product to protect it from corrosion or improve its appearance. Its techniques include painting, coating, plating, and polishing.
8. There are many different types of metal alloys, each with its unique properties and uses
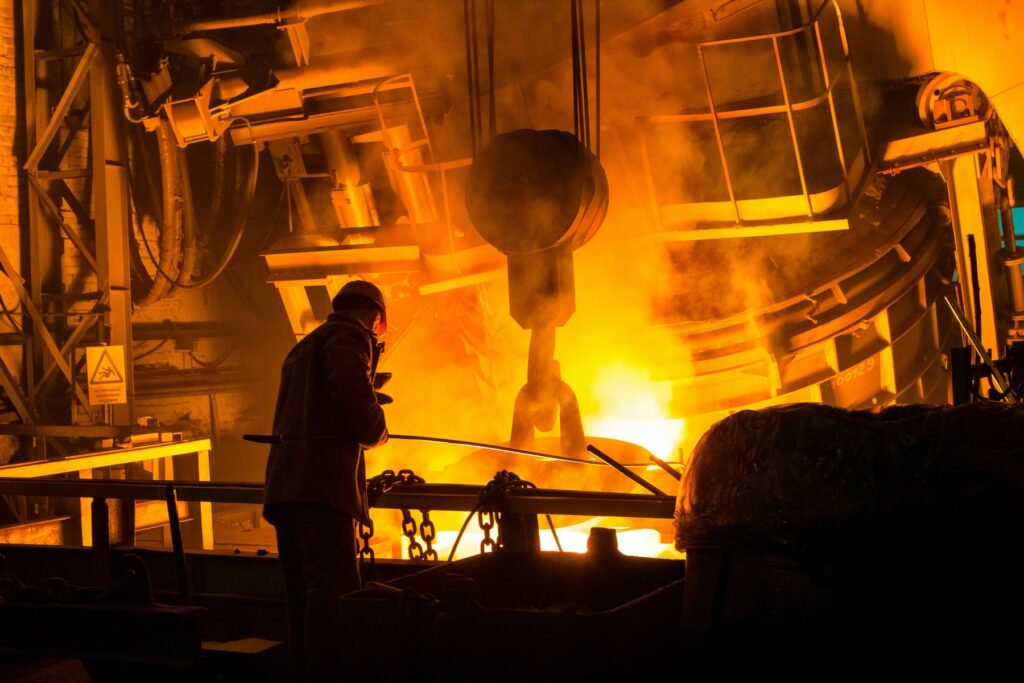
Metal alloys are materials composed of two or more metallic elements that are combined to create new properties and characteristics not found in their individual components.
One example of a widely used metal alloy is stainless steel. It contains at least 10.5% chromium, which ensures its unique corrosion-resistant properties. This makes stainless steel an ideal material for use in food processing, medical equipment, and other applications where corrosion resistance is critical.
Another example is titanium. It is a strong and lightweight material that is commonly used in aerospace and medical applications. This alloy is also corrosion-resistant and has a high strength-to-weight ratio, making it an ideal material for applications that require both strength and durability.
Other common metal alloys include brass, bronze, and aluminum. In addition to their unique properties, these materials can also be designed to have specific ones by adjusting their composition. For example, adding small amounts of certain elements to a metal alloy can improve its strength, ductility, or corrosion resistance.
9. Different types of metalworking can involve hazardous materials and processes
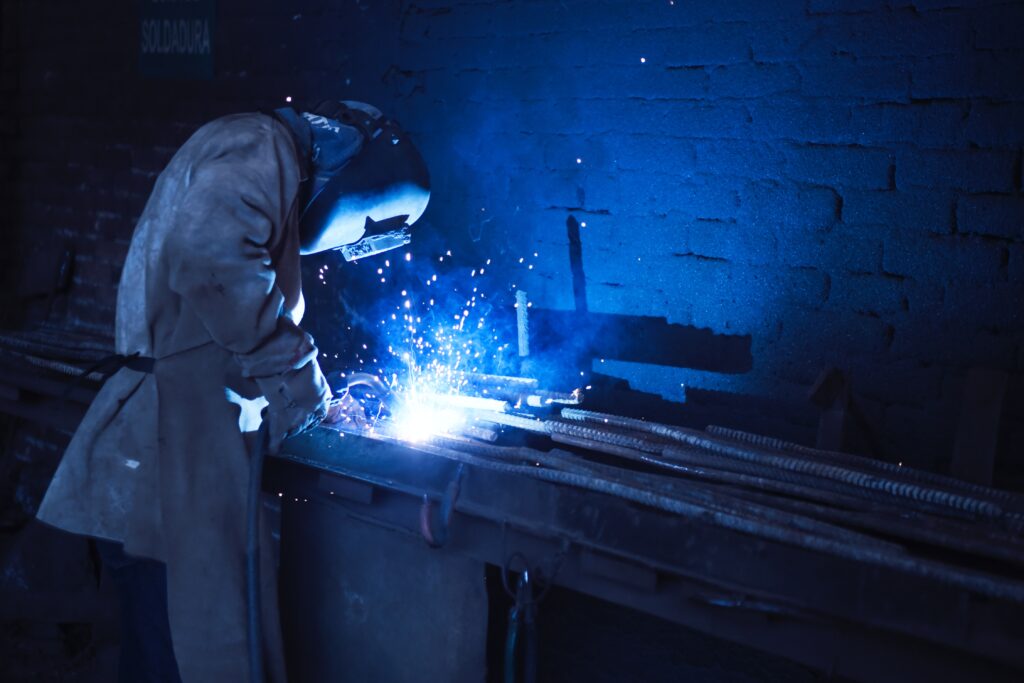
Processing metals requires working with a range of materials, such as iron, steel, aluminum, and titanium, which can pose various health and safety risks to workers.
For instance, welding produces fumes and gasses that are harmful if inhaled. These fumes can cause short-term effects such as dizziness, nausea, and eye irritation, as well as long-term effects like lung damage and cancer.
Molten metal is another hazard in the metalworking industry. Burns and other injuries can occur if workers come into contact with hot metal or sparks. To prevent these types of injuries, workers must wear appropriate protective gear such as heat-resistant gloves, jackets, and face shields.
Metalworking also involves the use of heavy machinery, such as grinders, saws, and drills, which can produce high noise levels. Prolonged exposure to these noise levels causes hearing damage, so workers must wear appropriate hearing protection.
10. Metalwork can be an environmentally friendly process
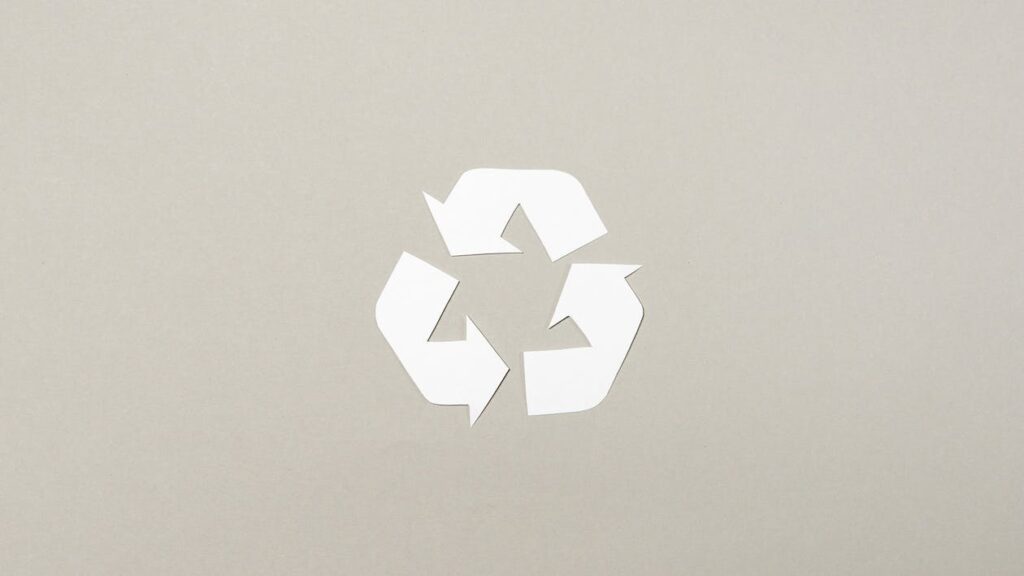
The production of new metal results in significant environmental impacts, including deforestation, air pollution, and water contamination. However, metalworking can be environmentally friendly when scrap metal is recycled, which reduces the need for mining and conserves resources.
The metal recycling process involves collecting, sorting, and processing scrap metal into reusable material. Metal can be recycled indefinitely without losing its properties, making it an ideal material for sustainable manufacturing. This process also requires less energy compared to the production of new metal. According to the United States Environmental Protection Agency, recycling aluminum saves 95% of the energy required to produce aluminum from bauxite ore.
Wrapping Up
Metalworking is a fascinating and complex industry that has evolved to become a vital aspect of modern society. It requires a wide range of skills and techniques, and it is used in a variety of industries. Whether you are creating a metal tool, building a skyscraper, or designing a new electronic device, metalworking services play a crucial role in making it possible. At RER, we do everything for the industry to evolve and develop, making the future closer to everyone.